Rotary Furnace
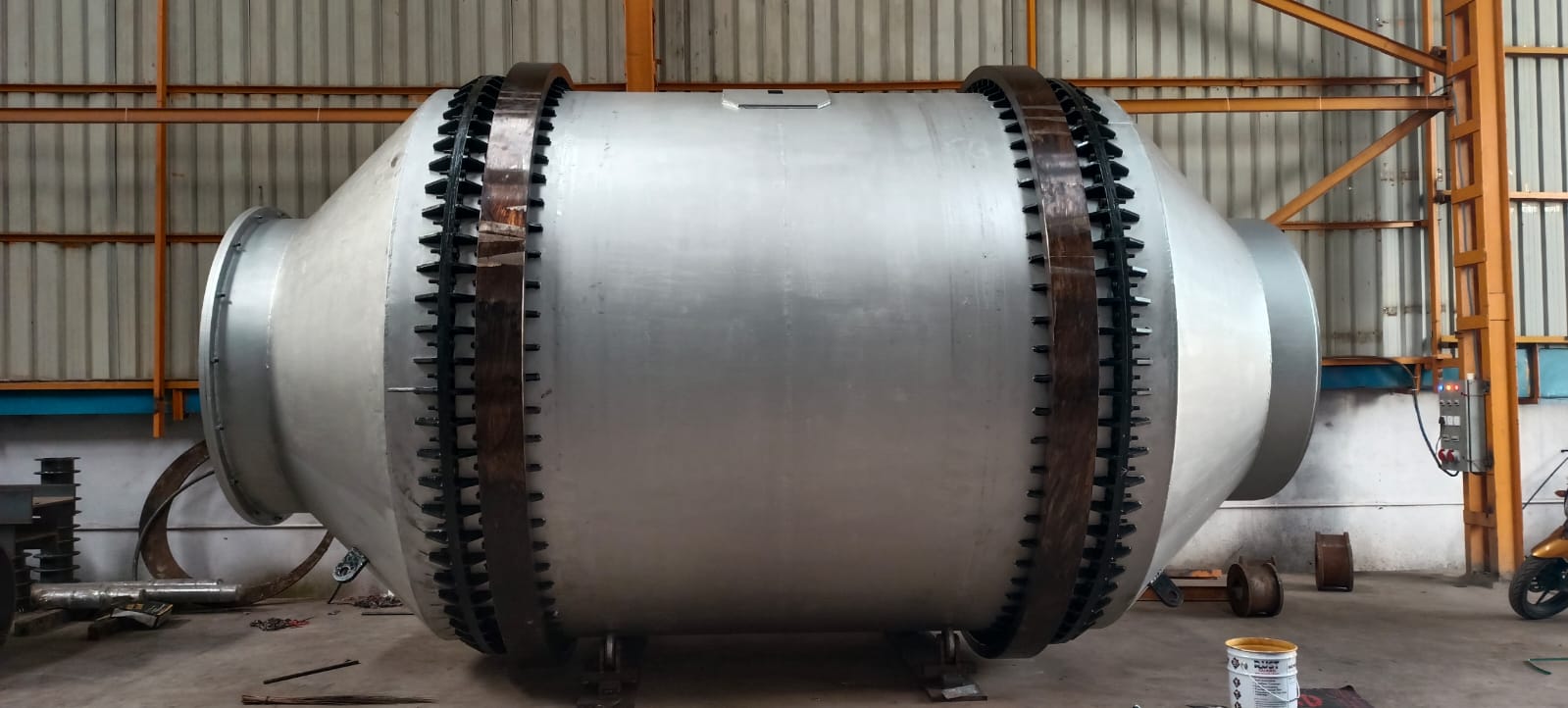
Raw materials required:
- Lead Acid Battery Scrap
- Lead dross
- Lead concentrate
- Lead Scrap
- Lead ash and other lead-bearing scraps
- Aluminum Scrape
Rotary Furnace for Lead and Aluminum Smelting: The Superior Choice
A rotary furnace is an essential industrial tool for the high-efficiency smelting of metals like lead and aluminum. This cylindrical, rotating furnace is designed to process a wide variety of raw materials, including scrap metal, ores, and dross, to extract valuable metals. The constant rotation of the furnace ensures even heat distribution and thorough mixing, making it the preferred technology for industries that require large-scale, consistent, and energy-efficient metal processing.
What is a Rotary Furnace?
A rotary furnace, also known as a rotary kiln, is a high-temperature processing unit that operates on the principle of continuous rotation. This movement facilitates uniform heat treatment, which is crucial for extracting metals from ores or refining scrap metal into usable forms. The furnace consists of a rotating cylindrical shell, typically lined with refractory material to withstand high temperatures and corrosive elements.
In lead and aluminum smelting, the rotary furnace is particularly advantageous due to its ability to handle both primary (from natural ore) and secondary (from recycled materials) smelting. The furnace is heated either by oil, gas, or electricity, reaching temperatures as high as 1400°C. This makes it ideal for the efficient recovery of metals in industries focused on sustainability and waste minimization.
Why is a Rotary Furnace Preferred Over a Static Furnace?
While static furnaces (also known as reverberatory or stationary furnaces) have been used in metal smelting for years, rotary furnaces have become the preferred choice due to several key advantages:
1. Superior Efficiency:
Better Heat Distribution: The constant rotation of a rotary furnace ensures uniform heat distribution throughout the material. This allows for faster, more efficient smelting compared to static furnaces, where heat often accumulates unevenly, leading to energy waste.
Higher Metal Recovery: Due to the efficient mixing and contact between the metal and the furnace lining, a rotary furnace can extract more metal from the same amount of raw material, making the process more cost-effective.
2. Versatility:
Rotary furnaces are highly adaptable to different feedstocks, whether it’s scrap, ores, or dross. This makes them ideal for both primary and secondary smelting processes. In contrast, static furnaces may struggle with certain materials, especially those with high moisture content or variability in size.
3. Environmental Benefits:
Rotary furnaces are more environmentally friendly compared to static furnaces, thanks to their lower fuel consumption and the ability to capture more metal from waste materials. The enhanced control over emissions and reduced fuel usage align with the increasing global emphasis on sustainable manufacturing processes.
4. Cost Efficiency:
The increased smelting speed, higher recovery rates, and reduced fuel consumption make rotary furnaces significantly more cost-effective than static furnaces in the long term. Even though the initial setup cost may be higher, the operational savings and improved productivity more than compensate for it.
5. Consistent Product Quality:
The rotary action ensures that the charge material is in constant motion, promoting even melting and a consistent end product. This consistency is harder to achieve in a static furnace, where certain parts of the material may melt unevenly.
Applications of Rotary Furnaces
Rotary furnaces are used across various industries, from recycling operations to large-scale metal production. Key applications include:
Lead Smelting: For both primary lead extraction from ore and secondary lead recovery from scrap and lead-acid batteries.
Aluminum Smelting: Ideal for recycling aluminum scrap, dross, and slag to produce high-quality aluminum ingots.
Other Metals: Rotary furnaces can also process zinc, copper, and various ferrous and non-ferrous metals.
- Working temperature: 1000-1200 Degree C
- Smelting: The Raw materials mixed with soda ash, iron turnings and charcoal are used for smelting.
- End products: Lead blocks
- Working temperature: 1000-1200 Degree C
- Smelting: The Raw materials mixed with soda ash, iron turnings and charcoal are used for smelting.
- End products: Lead blocks
Why Choose Us?
As a leading manufacturer of rotary furnaces for lead and aluminum smelting, we offer state-of-the-art technology designed for optimal performance and durability. Our rotary furnaces are engineered for energy efficiency, longevity, and ease of maintenance, ensuring that your investment delivers maximum returns over time.
With a strong focus on innovation and environmental sustainability, we help businesses reduce waste, improve metal recovery rates, and lower energy costs. Partner with us to take advantage of cutting-edge rotary furnace technology, customized to meet the unique demands of your operation.
Conclusion
When it comes to choosing a furnace for metal smelting, a rotary furnace stands out for its efficiency, cost-effectiveness, and superior metal recovery. By opting for a rotary furnace over a static furnace, manufacturers can significantly improve their production process while reducing environmental impact.
For high-performance lead and aluminum smelting solutions, our rotary furnaces deliver the best in modern industrial technology. Contact us today to learn more about how we can help optimize your metal smelting operations.
Rotary Furnace Shipping
Ready to transport
Rotary Furnace Installed
@ Client Site
Aries Fabricators & Engineers
#38-B1, Narayanapura Main Road, 2nd Phase, Peenya Industrial Area, Bangalore – 560058
Industrial Applications:
- Smelting of lead sourced from Lead Acid Battery Scrap
- Smelting of lead sourced from Lead Scrap
- Smelting of lead sourced from Lead concentrate
- Smelting of lead sourced from Lead dross
- Smelting of lead sourced from Lead ash